In mine planning, we know that modelling mining capacity using truck hours is important; it increases the accuracy and practicality of mine plans. This was discussed in more detail in our previous post.
In this article we take a look at another aspect of the problem which deals with moving waste to its final destination in the waste dump. In particular, we will explain how developing your mining and waste dump schedules in isolation may cause problems, and will discuss how integrated waste dump and pit schedule optimization, recently implemented in Minemax Scheduler, improves the accuracy and practicality of your strategic mine plans.
Waste Trucking Is Important
Trucking requirements vary according to the location of the mining block in the pit, so modelling mining capacity using truck hours based on cycle times and truck capacity is important. It enables us to set limits on available truck hours rather than on total movements in the schedule optimization, which helps to develop a more practical schedule.
Waste dump scheduling also has a significant influence on trucking requirements. So it is equally important to model waste movements using truck hours based on cycle times to the specific waste dump location in order to develop accurate schedules. This is even more critical for larger operations with bigger waste dumps and/or higher strip ratios, since higher waste volumes and/or longer waste hauls mean a higher proportion of the total trucking capacity needs to be allocated to waste movement.
Many open pit mines are effectively large-scale, bulk earthmoving operations where the valuable mineral that goes on to further processing can be only a relatively small proportion of the total material movement.
The Traditional Approach
Traditionally, mine planners focus their efforts on developing mine schedules with only rough consideration and approximations used for waste dumping. This can mean that whilst attempts are made to ensure that schedules are optimized for ore and waste extraction in order to find the best value, the optimization is restricted to a degree because it only includes estimated waste movements.
The detailed waste dumping schedule is typically then developed later on, as a separate process to the mine schedule optimization. Typically, two of the main approaches to estimate waste dumping are:
Considering Waste Movements Expressed in Tonnage
This basic approach uses a maximum material movement limit based on digging and hauling capability in tonnes per period and does not consider depth dependent waste trucking requirements from the pit out and to the waste dump at all. This approach will lead to the highest degree of inaccuracy.
Considering Waste Trucking to the Waste Dump Centroid
A more advanced approach is to consider waste trucking requirements on a per block basis from the pit to some average location in the waste dump. This is quite often the centroid of the waste dump. This means that we calculate waste truck hours based on cycle times from the correct location in the pit to the dump centroid. This method is more accurate than the basic approach but still has a considerable degree of inaccuracy.
Problems with the Traditional Approach
Unfortunately, many people are not aware of the risks associated with the traditional approach using estimated waste dumping. The problem is that if we carry out the detailed waste dump scheduling as a separate process after the extraction schedule is optimized, we might find out that the estimated truck fleet from the extraction schedule is very different to the truck numbers required to move the waste to the actual location on the waste dump.
If we overestimate the trucks in our schedule, this means that we will end up with unused trucks which would result in a loss of value. If we underestimate the trucks in our schedule, we won’t have enough trucks to move the waste, and the schedule will become impractical.
In both situations, we have to return to the mine scheduling process and re-adjust the original schedule to satisfy the newly identified trucking requirements. If we do this, there is a high chance that this new schedule will no longer be optimal and we are very likely to lose Net Present Value. So what can we do to avoid losing business value?
Integrated Waste and Pit Schedule Optimization
The Integrated Approach rectifies the imperfections of the traditional approach by integrating detailed waste and mine scheduling within one single optimization process. The Integrated Waste and Pit Schedule Optimization concept was first introduced in Minemax Scheduler 6.1. This concept is based on modelling a detailed waste dump design, divided into lifts and then further subdivided into waste dump blocks (or “cells”).
It is very easy to import a waste dump model into Minemax Scheduler using standard design package formats, and once imported, you can view the waste dump design in 3-D, together with the pit/pushback visualizations.
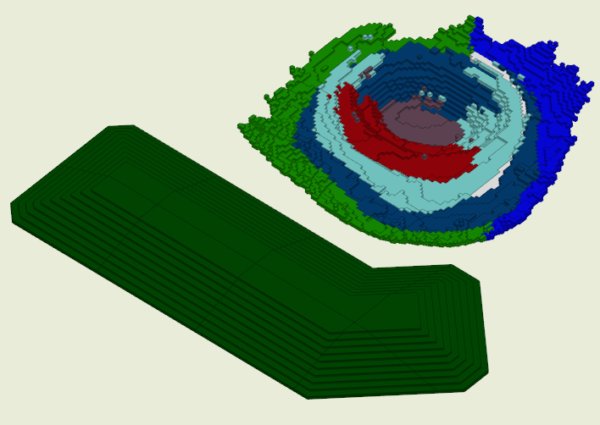
You can also set up precedences for the waste dump cells to ensure the correct horizontal and vertical construction sequence of the dump. By doing this, the waste dump cells with their associated storage capacities and physical location attributes can be included in the optimization algorithm, in a similar fashion to the pit blocks.
You can then let Minemax Scheduler find an optimal solution that jointly considers the block’s source locations as well as its range of possible final destinations. Using this integrated approach will lead to a truly optimal solution that maximizes the net present value of the project. The integrated approach is particularly beneficial for modelling accurate trucking requirements because we calculate truck hours based on correct cycle times to the final waste dump location rather than “rough estimates” to an arbitrary point.
This allows us to use the correct total truck hours as a maximum capacity constraint for the optimization process. To improve the accuracy even more, we can also use trucking costs as an input to the financial model used by Scheduler to make its optimization decisions. Not convinced yet? Let’s take a closer look at some examples.
Traditional vs Integrated Approach
To compare these two approaches, we modelled an example of a mine operation with one pit, one waste dump and one processing plant to optimize a 12-year schedule in Minemax Scheduler.
The Traditional Approach
First, we modelled our example using estimated waste trucking to demonstrate the traditional approach. For this, we used estimated cycle times from the block pit location out to a centroid of the waste dump, determined the total truck hours and used them to constrain the capacity of the schedule. Then we ran an optimization on the model to find the best schedule that maximizes NPV, and viewed reports with trucking requirements per time period.
The movement chart for the traditional approach shows an optimal schedule utilizing a maximum of 50 trucks to move the ore and waste material.
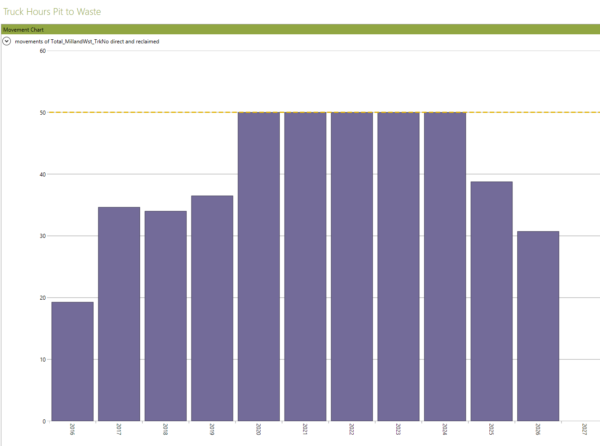
The Integrated Approach
Next, we modified the basic model using the integrated approach. We imported a detailed waste dump model split into separate dump lifts and smaller “cells” on each dump lift, set appropriate precedences between the cells and calculated waste truck hours based on cycle times to the individual cells in the waste dump. Then we optimized the model and viewed the reports with the movement chart showing the trucking requirements per year.
The movement chart for the integrated approach shows a need for up to two additional trucks between years 2010 and 2014 when compared to the traditional approach.
This means that if we used the traditional approach for this scenario, we would have underestimated the number of trucks in our schedule, leaving us one or two trucks short of being able to move all the material according to the planned schedule. So the mine plan that was produced using the traditional approach is in effect, not practically achievable.
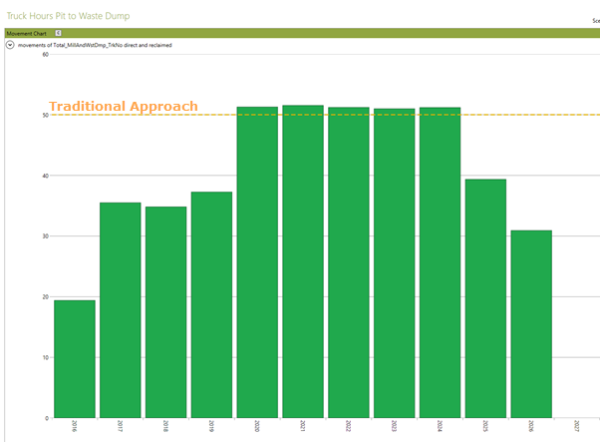
Total NPV Value Comparison
When we compare both schedules, the traditional approach estimates a higher NPV than the more accurate NPV calculated using the integrated approach. However, we have already seen that the schedule estimated using the traditional approach isn’t practical.
In fact, if we choose the traditional approach, we may end up with significantly less value than originally expected.
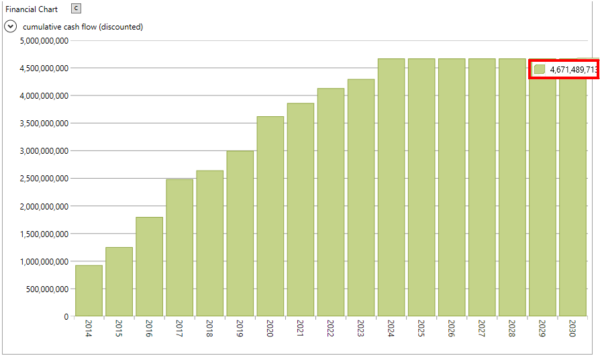
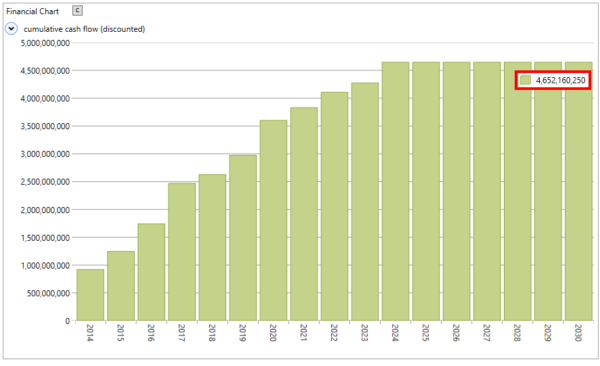
Summary
We have showed you via our basic waste dumping exercise how easy it is to produce more accurate and practical mine schedules when you use Minemax Scheduler to develop a model with detailed waste placement considering associated trucking requirements. With this integrated process, you will need to do less manual tweaking of schedules and ultimately you will have better utilization of your resources and greater confidence that your schedule is both optimal and practically achievable.
Modelling Complex Waste Dumps
Using Minemax Scheduler with integrated waste and pit schedule optimization, you can also handle more complex waste dumping scenarios in your mine planning projects and operations. For example, you can model multiple waste dump scenarios, and in-pit waste dumping (backfilling). You can also combine detailed waste dumping with alternative decisions where the classification of ore and waste material (or cut-off grade) is not predetermined but is rather an outcome of the schedule optimization.
Would you like to learn more about modelling complex waste dumps in Minemax Scheduler? Minemax provides a hands-on training course in advanced waste dump modelling techniques in Minemax Scheduler. Contact us for more details.