How many times have you developed a mine plan and later found that you needed more trucks?
Was that “later” point in time when your plan was used in operations? Or was it when the medium-term planners were working your long-term plan into their time frame?
What does it mean for both you and your company if your plan is not followed?
If the trucking numbers were slightly off, they probably followed parts of your plan. If they were way off, there‘s a good chance that they threw out your whole plan. All that hard work down the drain!
Operations needs to have faith in your mine plan if they are going to follow it. Being able to accurately model trucking in mine planning is the key to delivering mine plans that are practical. So where does the problem lie?
Mining Capacity Using Tonnes
Modelling mining capacity using tonnes can often give an inaccurate plan that cannot be followed in operations.
If we generate mine plans while thinking of fleet capacity and utilization in terms of tonnage, then we could be destined to fail.
When we constrain mining capacity using tonnage then we are not considering that trucking capacity is based upon:
- The load capacity of the trucks we use, and
- The expected time it will take to move the material from the pit to its final destination (cycle time)
As you can see in the charts below, just because the total material movement respects a maximum of 100MT, does not necessarily mean that our truck utilization follows the movements pattern.
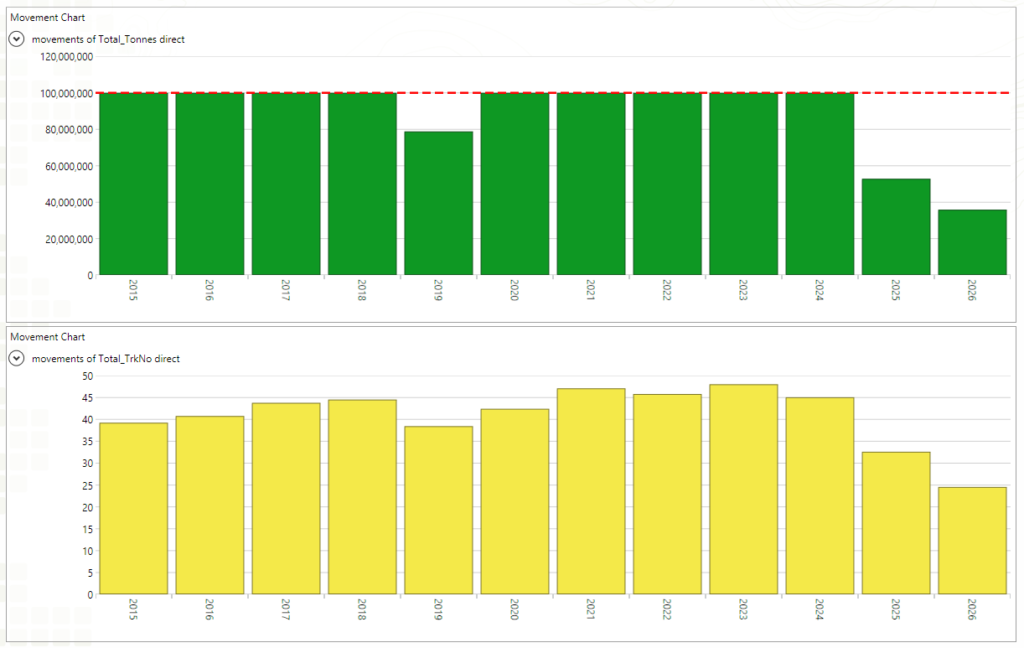
Mining Capacity Using Trucks and Cycle Times
Modelling mining capacity using truck hours increases the accuracy of a mine plan and makes it more useful for operations.
If we combine these two ideas of truck capacity and cycle times into something called truck hours, we can produce mine plans that have a better chance of being used in operations and adding value to the business.
We can calculate the total truck hours needed to move each block to any of its possible destinations such as mill, stockpile and waste dump.
\(BlockTruckHours=frac{Tonnes}{TruckLoad}times{CycleTime}\)
The capacity side of things in truck hours is straightforward. For a single fleet type, it is:
\(TruckCapacity=Total Truckstimes{Time Per Period}times{Availability}\)
Now we have everything we need to constrain the mining capacity using truck hours.
When we get this right, one of the interesting outcomes is that when trucking is the limiting factor, total movement can be quite variable. As long as the upper end of that variability doesn’t mean we are exceeding our excavator availability, then all is good. Operations won’t have any reason to throw this plan out the window.
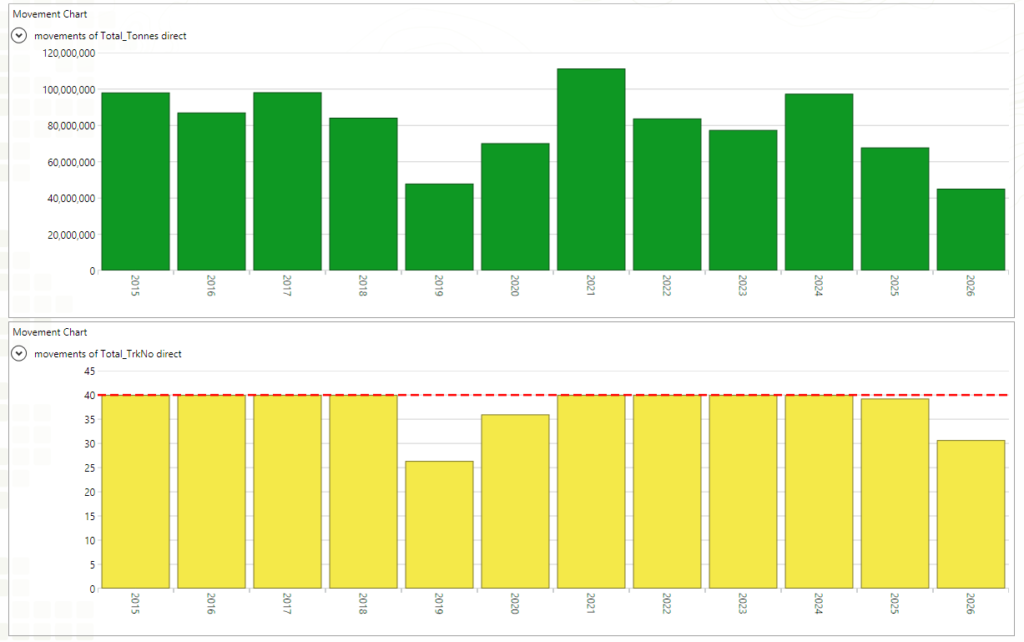
Putting it into Practice
If you are only using tonnage to model trucking capacity now, I hope this post has shown you what the pitfalls are. They can be remedied by following the steps above to incorporate truck hours into your mine planning process, resulting in a more practical mine plan.
If you would like to discuss your situation with us, please contact us.
If you want to learn a little more about the software used to generate these charts, you can download a free viewer version of Minemax Scheduler.
Download viewer